Technical Description
Technical Description of a Turbofan Engine
Oct 6, 2024
The Jet Engine
Aviation came to life with the Wright brother’s first flight in December 1903. The first planes used rudimentary engines with blades attached. These first planes were made from wood and fabric, as it allowed for lightweight construction. The first engines were inefficient and heavy, impractical for an aircraft to fly with. As the decade passed, aircraft and engine development paved the way for continuous, sustained flight. These new aircraft were not only strong enough to fly people but were used to transport cargo across the country. More substantial materials, such as aluminum alloys, were used as the engine developed. The development of planes caught the general public’s attention; by the end of 1920, aviation had cemented itself as an expanding industry, airports were popping up across the country, and heavy investment by entrepreneurs and the federal government gave rise to new technologies.
The federal government’s influential interest came from Europe’s looming threat of war. Shortly after a German U-boat struck down an American ship, the US joined World War One (WWI). WW1 was the first time aerial combat was seen; planes played a huge role, from supply lines to carpet bombing. As both sides of the war developed better engines, we saw the rise of new, more powerful aircraft engine designs, such as the radial engine, and the development of turbo/supercharged engines. This further improved the efficiency and reliability of airplanes, resulting in a heavy reliance on aircraft during the war.
Similarly, in World War Two (WW2), aircraft development was heavily influenced and dependent on government intervention. The US joined WW2 because a squadron of Japanese aircraft bombed Pearl Harbor. A decade prior, it would have been a fantasy to see planes cross the Pacific Ocean, let alone go cross-continental. Aircraft technology has advanced over the last few decades, making once-believed feats achievable. We saw the rise of subsonic aircraft capable of flying above 30,000ft going cross-continental. Undoubtedly, airplanes played a massive role in the development of the war both in mainland Europe and the Pacific. In the Pacific, theaters were fought with aircraft carriers, acting as runways for planes to take off/land and fueling stations. WW2 concluded with the Boeing B-29 Superfortress Enola Gay dropping the first and only pair of atomic bombs on Japan.
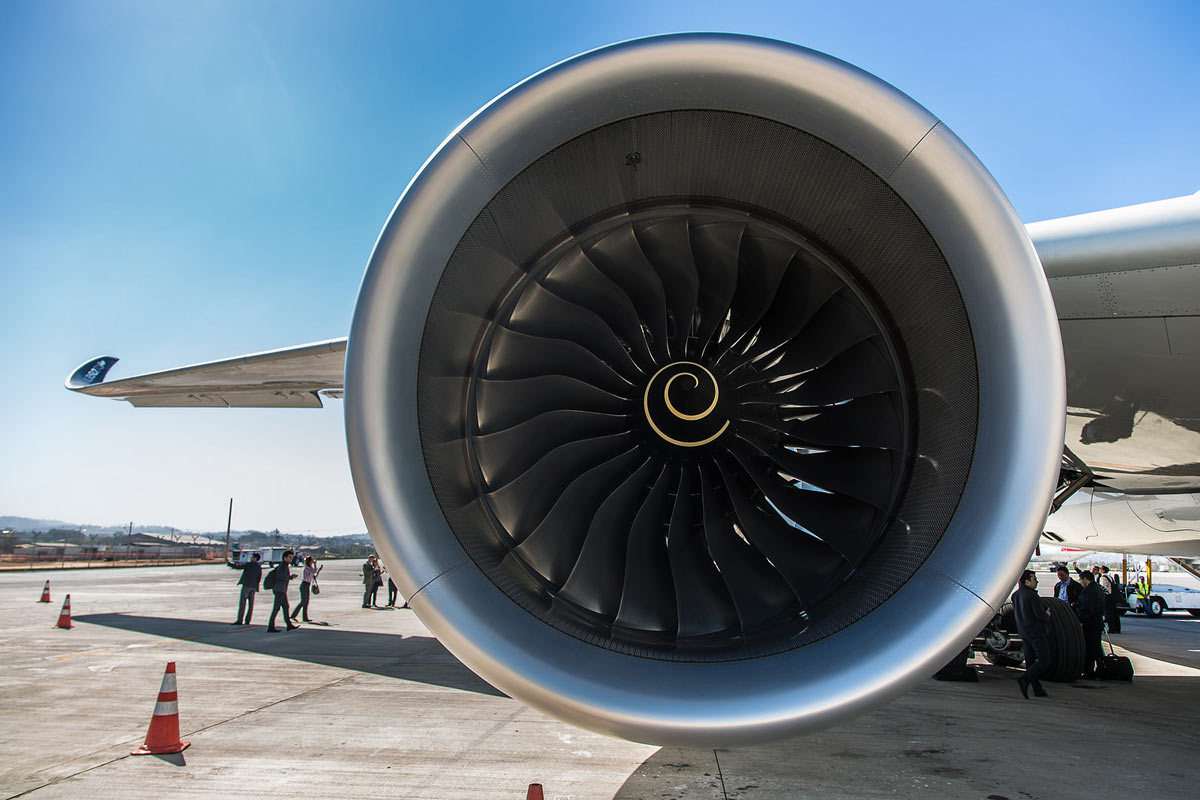
Americans and the British are not the only ones heavily researching and developing new aircraft technologies. The Germans made a revolutionary breakthrough in engine and aircraft design. During the mid-30s, the German Reich released the first supersonic aircraft with a new engine design; the Germans developed the first gas turbine engines capable of pushing aircraft faster with a more compact engine. The first gas turbine engine was used on the Heinkel He 178, “Something just flew past us, as if we were standing still,” Described an Allied pilot; they had just seen the first fighter jet. After the war ended, the US imported German scientists to develop the first American Turbine engine. As the decade ended, the Americans developed their first supersonic aircraft, the BellX-1, which took flight on October 14, 1947, at a top speed of 700 miles per hour (Mach 1.06) at 43,000 feet. Since then, we have continuously improved the gas turbine engine(GTE); all modern aircraft rely on a variation of German invention. Today, the most efficient variation of the GTE is the TurboFan, an engine similar to the first ones produced, except the turboFan employs a fan with an average diameter of 6-8ft capable of producing up to 50,000 horsepower.
The engine has five main sections: the Intake, Compressor, Burner, Turbine, and Exhaust.
Inlet
The inlet is known as the mouth of the engine, and it is where all the air enters. It is designed so air can flow into the engine with minimal effort at sufficient volume. Unlike other turbine engines, Turbo Fans have a massive fan at the inlet, also called the Low Pressure (LP) Fan, that generates up to 80% of the thrust! The LP fan accelerates large volumes of air at slow speeds, resulting in a high-efficiency, low-noise-pollution engine. Turbo Fan engines use the high bypass air principle to direct where the incoming air needs to go. The high bypass air principle splits incoming air into two ways: air goes through or around the engine’s core. Turbofan engines reach bypass ratios of 1:18; for every molecule of air that enters the core, 18 air molecules go around. Air that enters the core goes through the remaining four stages; it gets compressed, mixed with fuel, ignited, accelerated, and expelled. The air around the core may support combustion, but it mainly serves to keep the combustion temperatures at a minimum to prevent the metal from warping and cracking. On top of that, the air around the core is colder; when it meets with the hot exhaust at the end, it helps cool down the exhaust, which allows noise pollution to be kept at a minimum.
The LP fan generates thrust and protects the compressor from foreign object damage (FOD). FOD is any material or substance not meant to be ingested by the engine. Items that do enter may cause total engine failure, so the LP fan must be made of strong but light materials such as carbon fiber, aluminum, and titanium.
Compressor
The primary purpose of the compressor is to compress the incoming air from the inlet and supply it to the combustion chamber. There are two types of compressors: Axial and Centrifugal flow. An Axial flow compressor uses rotors and stators—a set of rotors and stators makes up a Stage in the compressor. Stators are part of the compressor casing; they are stationary blades designed to slow the incoming air while increasing pressure. On the other hand, the rotor is attached to a rotating shaft, helping improve the air velocity after the stator has slowed it down.
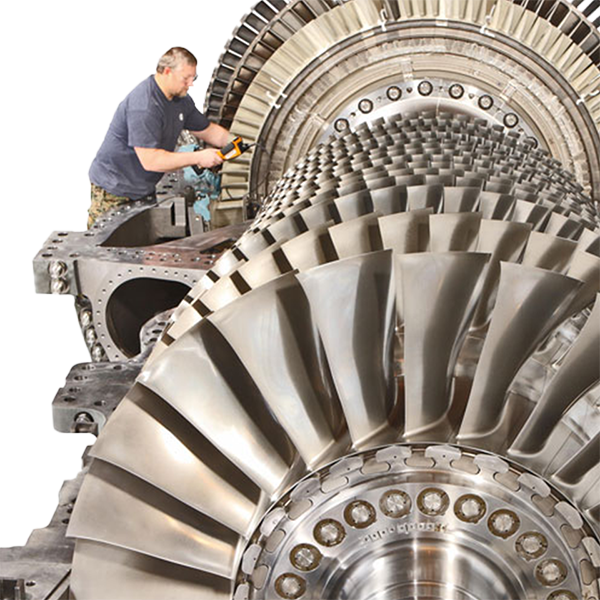
We need the air to flow uninterrupted through the compressor to avoid a Stall. A stall is an interrupted stream of air, like an engine beginning to choke. Compressor stalls lock the compressor, preventing the rotors from spinning. Without constant airflow, no power can be extracted, and the engine shuts down mid-flight. This poses a safety risk to the passengers on board, as the engine may be restarted in flight to provide stability.
We want to increase the incoming air pressure to extract the maximum power. Since a pressure increase is correlated to a rise in potential energy when mixed with the fuel, it releases tremendous power that the turbine collects. (More on that in the turbine section). As the pressure of a fluid increases, so does its temperature, known as the Bournulies principle. Modern aircraft extract hot air for anti-icing, cabin pressurization, and environmental control. The hot compressed air runs through the leading edge of the wings to prevent moisture from freezing on the wing, decreasing performance. Cabin pressurization is essential to remain conscious at 40,000ft. It prevents one from feeling unwell by simulating the pressure at sea level. Since the temperature of the compressed air gets so hot when mixed with the cold air at high altitudes, we can control the temperature in the cabin.
Burner

The burner section is the hottest section of the engine and must constantly withstand temperatures of 2000°C. The cold bypass air creates a layer of air between the hot gas and the combustion liner, preventing the walls from cracking or melting. As the air exits the compressor section, it swirls while being sprayed with fuel by the jet nozzles. The swirling of the air allows for a homogenous mixture that is even throughout. This prevents hot spots on the turbine nozzle or carbon deposits on the turbine blades.
Cars use spark plugs to ignite the fuel and air in the cylinder to create power. However, jet engines use a glow plug, a beefier, more potent version of a spark plug. Unlike cars, jet engines must be able to operate in cold, wet climates. Typically, glow plugs are used only when starting up the engine; after that, they are shut down, as the expanding hot gas from within the chamber is enough to ignite the incoming stream of air from the compressor.
Turbine
The turbine must be able to extract power from the hot gases. To do this, the exiting gas from the burner is angled so that as it expands, it pushes all the sets of rotors. Similar to the rotors of the compressor, they allow the gas to accelerate and decrease its pressure. The rotors are attached to a shaft that connects the compressor and turbine. Typical GTEs use three stages to extract the available power from the exhaust. Depending on the type of engine design, two shafts may be employed. Some engines have low-pressure and high-pressure compressors. This implies the existence of low-pressure and high-pressure turbines. The first set of stages in the turbine section is known as the high pressure; as they rotate, so does the high-pressure compressor, and as the low-pressure turbine spins, so does the LP Fan.
During engine start-up, the engine spools the low-pressure turbine, which requires the least energy to spool to operating speed. The compressor creates a vacuum by rotating the turbine, drawing in the surrounding air.
Exhaust
Finally, the exhaust section is designed to combine the cold bypass air with the hot exhaust. The cold bypass air cools the hot gas, reducing engine noise. The exhaust section is made of the turbine nozzle and the shape of the exhaust. We want to expel the gases at a high velocity. To do this, the burnout principle is employed again; as the velocity increases, the pressure and temperature decrease. The turbine nozzle creates a diverging duct at the exhaust against the engine’s casing. A diverging duct expands in diameter; the gas would also develop since it is increasing in size. As the gas expands, it loses pressure, and because pressure decreases, its exit velocity increases. We need the exit velocity to be as high as possible to create power; in turbofan engines, the exhaust only makes up 20% of the trust. Despite the core only creating up to 20% of the thrust, the core is crucial for the engine’s power development.
Conclusion
Technological advancements have allowed for the development and increased reliability of aircraft technology. We’ve seen engines push aircraft beyond their limits; the North American X-15 is the world’s fastest piloted aircraft, reaching speeds of Mach 6.72. The development of engines has paved the way for supersonic commercial flights with the development of Concorde, which has cruising speeds of Mach 2. Aviation is an ever-expanding industry, and innovations will allow for new developments in commercial aviation.
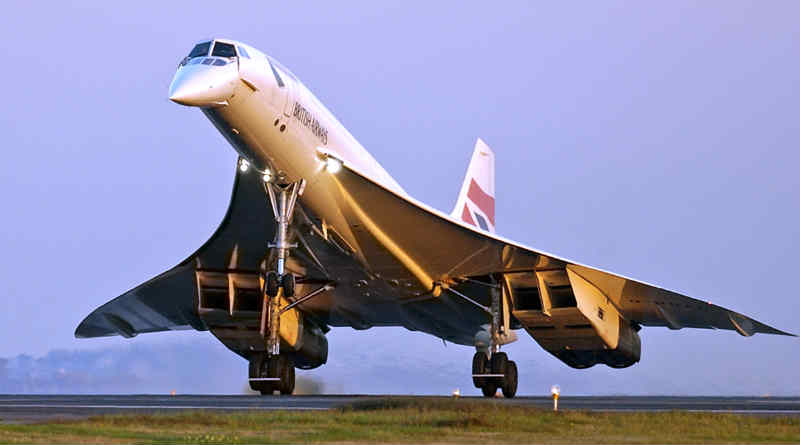